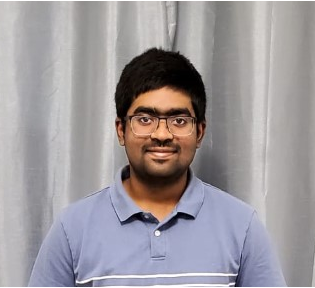
Author: Ganesh Mathiarasu
Published: 10 Mar 2023
Description: Second iteration of ring body made using SLA
Manufacturing SLA Rings (Mar 6-10)
Due to extremely tight constraints with regards to the space inside the ring to precisely locate the different sensors, the mechanical structure of the ring was heavily influenced with the dimensions of the different PCB tiles (and its components), overall positioning of the tiles relative to each other, and wiring. A change in any one of these categories would result in a minor modification to the ring’s design, since the ultimate goal was to keep the overall dimensions as small and sleek as possible.
Stereolithography, commonly known as SLA printing, proved to be efficient during the prototyping stage. It involves using a laser beam to photochemically solidify liquid photopolymer resin. This results in a product with higher quality, with smooth surfaces and intricate details. It also provided us with the opportunity to select from a variety of different photopolymer resin materials, colours and finishes. This level of intricacy would not have been possible with regular PLA 3D printers.
One issue we ran into during the curing process was that the inner rings formed with either transparent or white resin would be prone to cracking. The root cause of this was due to an inconsistent surface of the build plate and the damages to the surface of specific tanks. The problem was resolved by limiting colours to matte black and grey.
Big challenge: avoiding cracks
Additionally, the concentration and density of the support structures were also reduced in order to reduce the amount of imperfections caused by them on the surfaces of the ring. These imperfections were later removed during post-processing to achieve a sleek and finished look.